Digital innovation has pushed its way into virtually every industry: Chatbots have changed online customer service, fast and simple checkouts have revolutionized ecommerce, and biometric security has transformed banking apps. However, if there’s one industry that has stuck to its traditional approaches, it’s manufacturing.
As many organizations’ budgets get tighter, teams get leaner, while revenue goals rise higher, the need for heightened efficiency, increased productivity, and a stronger competitive edge means there’s an opportunity for manufacturing to throw away old and tired processes and embrace digitization.
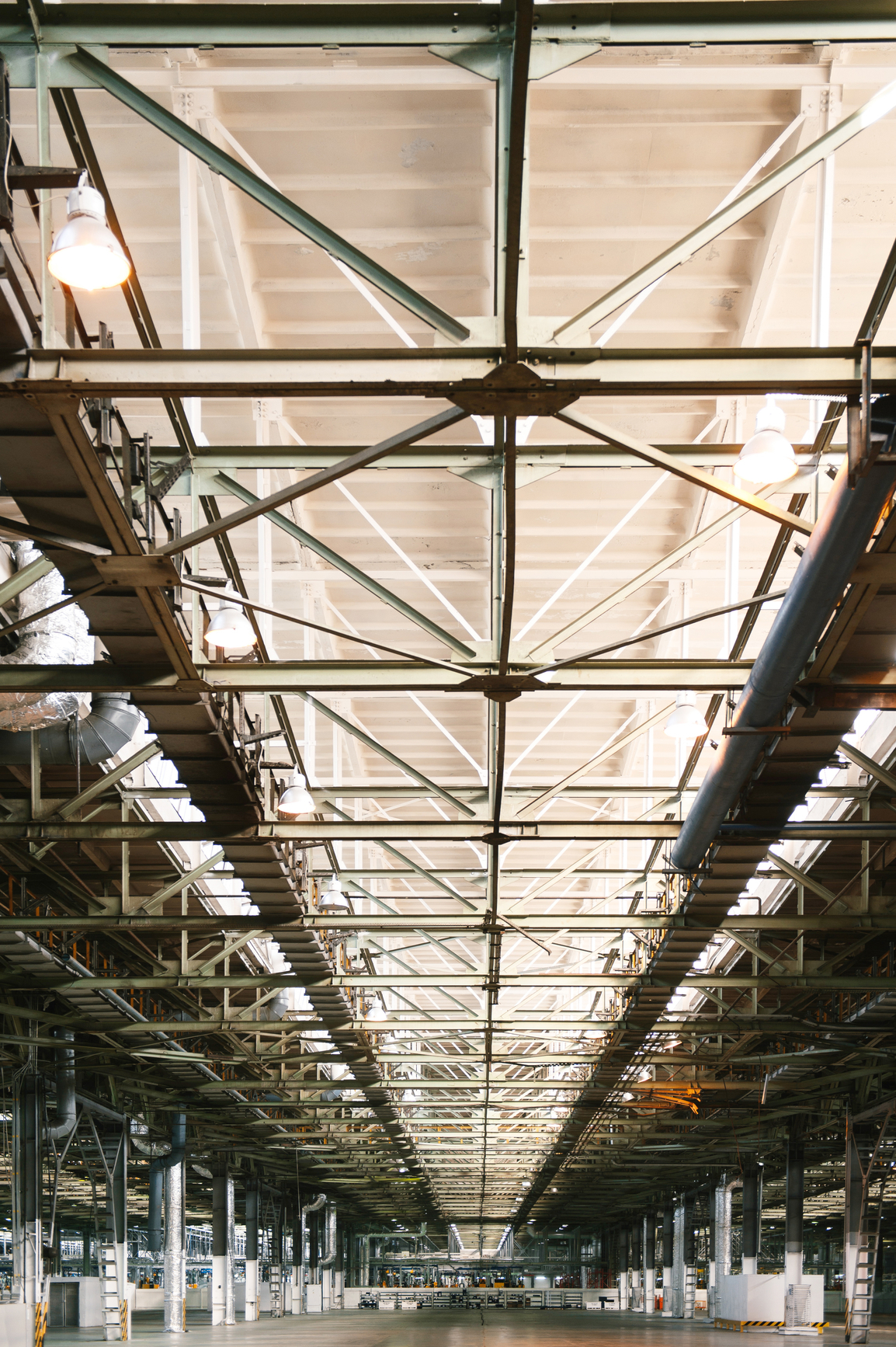
For manufacturers wondering where to start with digital innovation, these are the top three points that highlight the need for a technology revolution:
1. Enhancing Operational Efficiency With Automation
Recent studies reveal that companies lose 30% of revenue due to operational inefficiencies. Typically, the goal of any manufacturer is to produce as many units as they can with as few defects as possible. If Manufacturer A produces one million units per year with an 80% defect rate, they are making less money and are far less efficient than Manufacturer B, which aims to produce 800,000 units of the same product per year with a 1% defect rate.
One of the primary advantages of digital innovation is its ability to streamline operations and boost efficiency across a production cycle. Artificial Intelligence (AI), the Internet of Things (IoT) and robotic automation have afforded many industries the ability to optimize their resources, minimize downtime, reduce waste, and allow employees to focus on core business functions without being bogged down by tedious and time-consuming tasks.
For example, implementing IoT-enabled sensors on machinery and equipment allows manufacturers to collect real-time data on performance. Using these insights, leadership can be proactive in troubleshooting issues before the equipment breaks down, pauses operations, and turns into a costly problem. By promoting proactivity and continuous operations, manufacturers can minimize downtime and maximize production output.
Manufacturers have to manage supply chains, address consumer demand, and pivot with market fluctuations every day. This is where AI allows organizations to rapidly collect and analyze data that delivers actionable insights to optimize production.
Lastly, robotic automation provides opportunities to streamline repetitive and labor-intensive tasks, freeing up humans to focus on added-value business functions. Whether you’re a big or small manufacturer, there is always a need to be more strategic with day-to-day activities. In the long run, adding robotics to your manufacturing process may foster a more productive and dynamic workforce.
2. Reinventing Quality Assurance
Quality assurance (QA) is a top priority for manufacturers, as their reputation often relies on consistent, top-notch products being delivered to customers and wholesalers. Traditionally, QA responsibilities fell to the employees working on the floor and production lines. Today, IoT software combined with AI-driven analytics improves real-time monitoring and provides predictive maintenance strategies that can detect defects at any stage of the production process.
Updating modern QA software allows manufacturers to offload the hefty and expensive task of monitoring and identifying product defects. Technology can continuously monitor production lines and alert employees to take proactive actions to prevent and reduce defects, which will minimize product recalls in the long run. Additionally, the right tech tools will detect surface defects, dimensional inaccuracies, and assembly errors with precision and speed.
Another modern QA strategy to consider includes implementing AI-powered systems that analyze large amounts of production data to identify quality issues and patterns. Once a foundational database is established, the algorithm can create predictive models that anticipate quality issues before they occur and enable manufacturers to maintain product integrity and consistency.
3. Customization for Customer-Centricity
Gone are the days of one-size-fits-all strategies. Driven by heightened consumer expectations and preferences for personalization, digital innovation empowers manufacturers to deliver tailored solutions and products.
Digital technologies such as Augmented Reality (AR) and Virtual Reality (VR) are rapidly rising across industries as a way to provide interactive experiences and allow consumers to visualize products in real time. Consumers don’t just want to create and view a custom couch online, they want to see it in their living room. As a result, AR and VR technologies enable manufacturers to engage customers throughout the design and purchasing process, fostering deeper brand connections and driving sales.
With advanced data analytics tools that produce actionable insights, manufacturers can look through the window at modern consumer preferences, behaviors, and purchasing patterns. By leveraging this knowledge, manufacturers can develop personalized offerings that enhance customer satisfaction and loyalty.
Conclusion
The manufacturing industry is on the edge of a digital revolution, with ample opportunities to design and implement technology to improve processes and quality control drastically improving customer experiences and satisfaction and ultimately increasing profitability. That is why digitization holds the key to unlocking a new era of manufacturing, one that is competitive, innovative and ripe for new opportunities.