Ensuring product quality through machine learning for Altia
Altia is a leading Nordic alcoholic beverage brand company operating in the wines and spirits markets in the Nordic countries, Estonia and Latvia. They produce, import, market, sell and distribute both own and partner brand beverages. Altia also exports alcoholic beverages to approximately 30 countries, mostly located in Europe, Asia and North America. Altia’s net sales in 2017 were EUR 359.0 million and the company employs about 700 professionals.
Altia wanted to improve quality assurance by automating the fault detection further, thus giving the quality assurance team the possibility to focus on more challenging tasks. With raised accuracy, waste would also be reduced, as the production line can be stopped and fixed if errors occur.
Image recognition to the rescue
We wanted to investigate if machine learning could produce a more accurate result than the human inspector. A cloud-based and on-premise solution were both used in order to test accuracy, and over 1200 images were used as a training set for the AI. The end results: near 100 % accuracy in recognition in both the cloud and on-premise solutions. Altia now has the capability to divert quality inspection resources to more complex matters. We are currently implementing the solution at the Rajamäki factory.
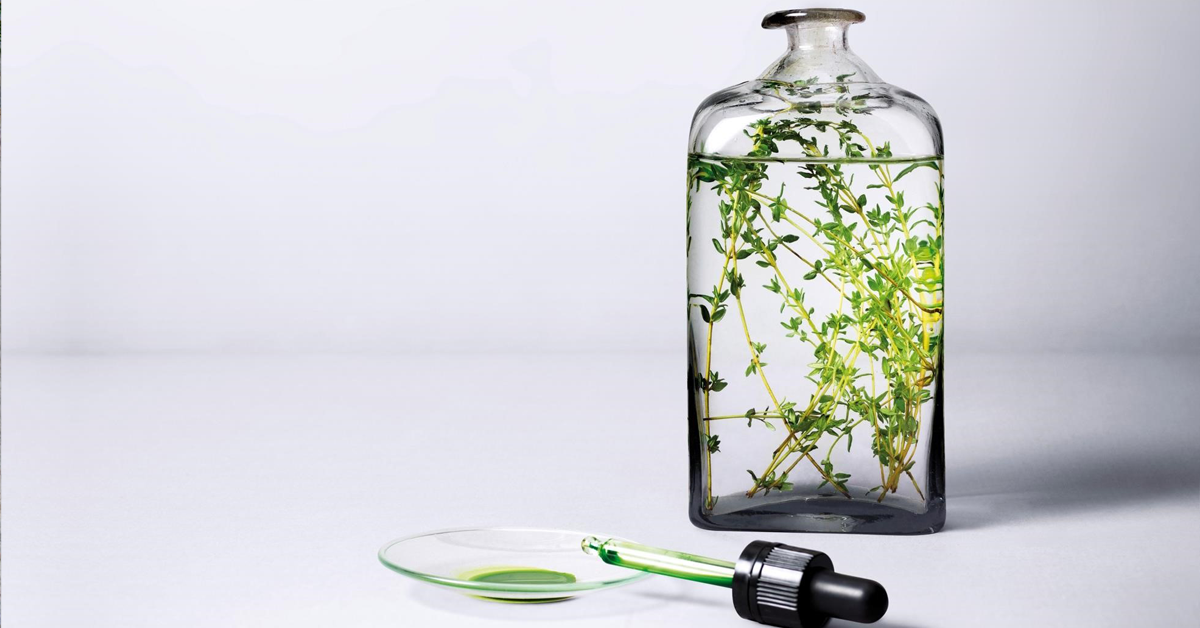
Ensuring quality of products by machine learning in Altia’s Rajamäki factory
Altia's historic bottling factory in Rajamäki has been in production since 1888. A total of 800 different wines and spirits, up to 70 million liters a year, is produced in the factory. There are eight production lines at use at the factory, which produce different products at different times.
Altia has a very strict process for product quality. Automatic inspection can detect missing labels, faulty closures or deficient fill level. However, manual inspection is needed in 8 production lines to detect other issues. Overseeing the production lines in order to weed out faulty bottles is a manual and boring process. Manual inspection requires the full attention of one person per production line, where the production speed can be up to 18 000 bottles per hour.
Altia wanted to improve quality assurance by automating the fault detection further, thus giving the quality assurance team the possibility to focus on more challenging tasks. With raised accuracy, waste would also be reduced, as the production line can be stopped and fixed if errors occur.
In the proof of concept, Bilot and Altia realized that this problem can be solved with image recognition and machine learning.
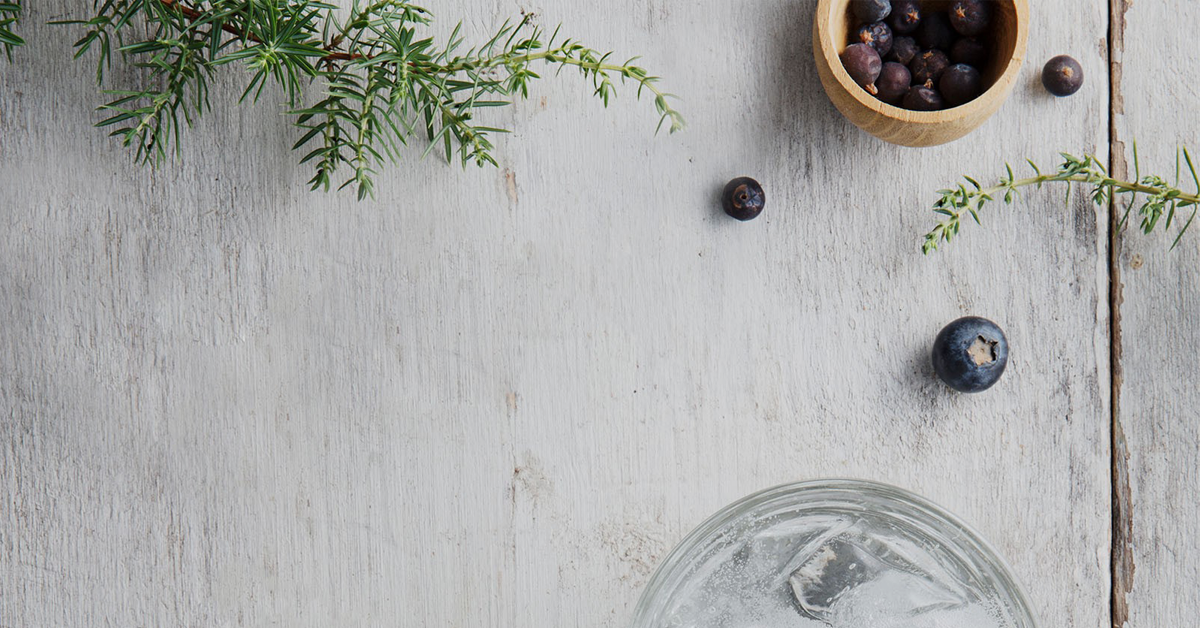
Expertise used
Ensuring quality of products by machine learning in Altia’s Rajamäki factory
- Scope the problem for proof of concept
- Create the data set to test drive the algorithms
- Train their people in machine learning problem solving
- Build the prototype into the cloud and on-premise for comparison purposes
- Create the business decision materials and justifications for the actual project
Technologies:
- Azure Cognitive Services – Cloud solution
- Keras & TensorFlow – On-premise solution
- Custom firmware for Canon 60D camera